소재부터 완제품까지 수직 계열화…그라파이트 방열시트 국산화로 쌓은 기술력 음극재에 적용
[인터뷰]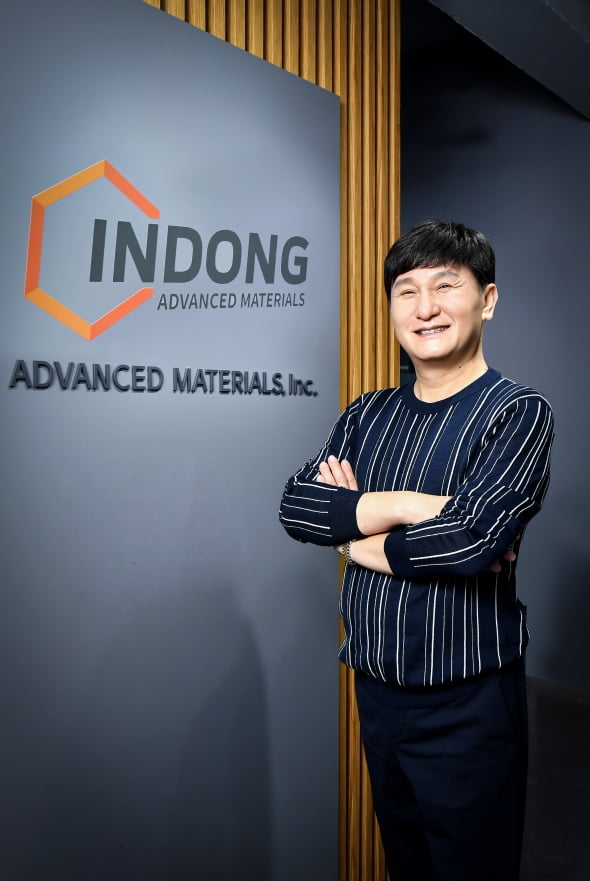
최근 장외주식시장(K-OTC)을 뜨겁게 달군 기업이 있다. 거래 첫날 400% 상승한데 이어 상장 이후 한 달이 지난 현재까지 거래 대금 기준 1위를 차지하고 있는 인동첨단소재다.
인동첨단소재는 ‘복합 그라파이트 방열 시트’를 시작으로 2차전지 음극 소재인 ‘구상 복합화 흑연’을 개발·제조·판매하는 소재 전문 기업이다. 지난해 음극재업계의 화두인 실리콘 복합 음극재를 생산하는 FIC신소재를 창립하며 실리콘 복합 음극재 대량 생산에도 도전했다. 향후 완성품을 제조하는 유로셀을 통해 기존 용량보다 150~200% 증가한 고용량 배터리를 출시한다는 구상이다.
수년간 축적한 탄소 미세 분말 제조 기술 등 원천 기술로 배터리 시장에 출사표를 던진 유성운 인동첨단소재 대표이사를 서울시 서초구에 있는 사무실에서 만났다. 유 대표는 배터리 소재 기업인 인동첨단소재를 발판으로 소재부터 완성품 제조까지 2차전지의 밸류 체인을 강화해 나갈 것이라고 포부를 밝혔다.
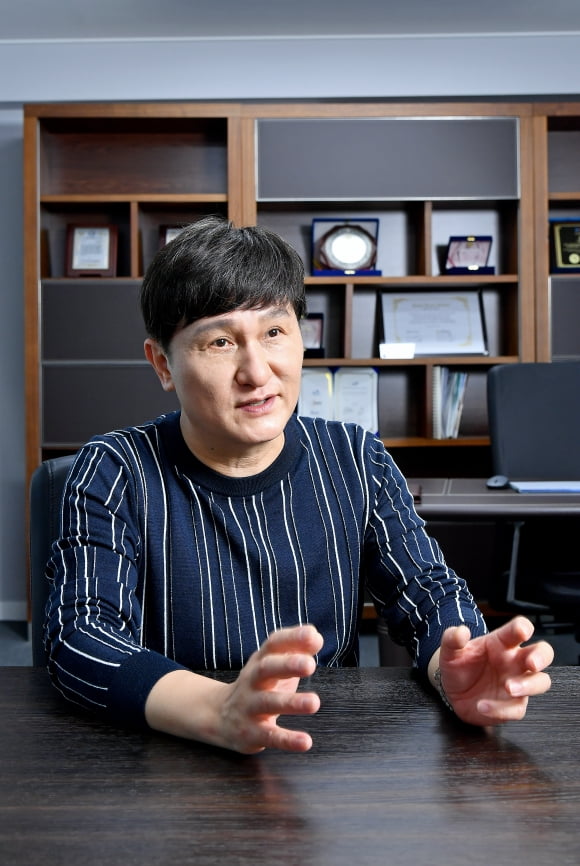
“주주들이 주식을 제도화된 시장을 통해 안전하게 거래할 수 있도록 K-OTC 시장에 진입하기로 결정했다. 향후 기업공개(IPO)를 통한 상장으로 대규모 자금이 유입되면 생산 설비에 투자해 규모를 확대할 계획이다. 이미 실리콘 복합 음극재 원천 기술에 대한 검증을 완료하고 가능성을 확인했으니 남은 것은 생산 설비를 늘려 공급을 원활하게 하는 것이다.”
-방열에서 최근 배터리로 사업 영역을 확장했다.
“방열 소재(전자기기에서 발생한 열을 방산하는 소재)를 하면서 흑연 가공 기술을 축적했다. 흑연으로 할 수 있는 일을 찾다 보니 배터리로 사업을 확장하게 됐다. 음극재는 흑연을 갖고 만드는데 심각한 문제가 있었다. 로스(loss)율이 너무 컸다. 흑연을 가공하면 30%만 음극재로 사용되고 70%가 부산물로 버려진다. 음극재로 사용되기 위해서는 10마이크로미터(㎛)의 구형 흑연이 필요한데 균일한 품질을 얻기 위해선 균일한 크기의 10㎛의 흑연만 필요하므로 10㎛의 크기가 아닌 분쇄물 70%는 부산물로 버리는 것이다. 이 70%를 잡으면 승산이 있겠다 싶어 개발에 나섰다.”
-버려지는 부산물을 어떻게 사업화했나.
“인동첨단소재가 보유한 게 바로 독보적 분쇄 기술이다. 카본을 방열 시트로 만들기 위해선 10㎛ 이하로 분쇄해야 하는데 강철보다 강한 강도를 지닌 카본을 분쇄할 수 있는 장비는 세계 그 어디에도 없었다. 3년의 노력 끝에 분쇄 장비를 자체 개발해 분쇄에 성공했고 이를 통해 한국 최초로 그라파이트 시트를 국산화할 수 있었다. 이 분쇄 장비를 버려지는 흑연 70%에 사용해 음극재를 만들기로 했다. 버려지는 70%를 일반적으로 사용하는 장비로 분쇄했을 때 입자가 5~300㎛ 정도인데, 자체 장비로 흑연을 분쇄한 결과 부산물 전체를 1~10㎛ 로 균일하게 분쇄할 수 있었다. 부산물을 재가공해 음극 소재를 생산해낸 것이다. 1~10㎛로 균일하게 분쇄된 카본을 구 형태로 재조립하여 리튬이온전지의 음극재 기술 중 마지막 완성 기술로 불리는 구상조립흑연 기술을 실현했다.”
-구상 조립 흑연 기술이 뛰어난 이유는 뭔가.
“전기차 등으로 배터리 쓰임새가 커지면서 대용량 배터리를 필요로 하는데 흔히 쓰는 리튬 이온 전지에서는 실상 용량을 올리는 게 거의 불가능하다. 전혀 다른 소재를 써야만 용량을 키울 수 있는데, 과학자들이 찾아낸 소재가 바로 실리콘이다. 흑연 음극재에 실리콘을 첨가하면 배터리 충전 용량이 증가하고 속도가 빨라진다. 그 대신 실리콘은 팽창률이 400%에 달해 충전과 방전을 반복하면 깨져 버리는 단점이 있어 이 팽창을 제어하는 기술이 필요하다. 우리가 만든 구상 복합화 흑연은 미분화된 입자로 구성돼 실리콘계 음극재의 부피 팽창을 최소화할 수 있었다. 실리콘의 저장성과 흑연의 안정성을 모두 갖춘 음극재의 원료다. 폐기물을 활용했다는 점에서 원재료비를 대폭 절감해 가격 경쟁력을 갖춘 것은 물론 고용량의 배터리를 만들 수 있다는 점에서 기존 음극재의 단점을 해결하는 기술이다. 인동첨단소재가 상용화한다면 배터리 음극재 시장에 큰 지각변동을 가져올 것이다.”
-실제 생산에도 나섰나.
“새로운 배터리를 만들려고 하니 소재부터 완성품까지 모든 것을 갖춰야 했다. 소재만으로는 검증할 방법이 없었다. 완성품에 소재를 넣어 동작돼야 이 소재가 문제가 없다는 것을 증명할 수 있다. 그래서 유로셀과 FIC신소재 등 두 개의 회사를 차례대로 설립했다. 인동첨단소재가 70%의 부산물을 가져다 1~10㎛로 분쇄하면 이를 FIC신소재가 실리콘과 섞어 실리콘 흑연 복합 음극재를 만든다. 이 실리콘 흑연 복합 음극재를 이용해 유로셀은 기존 용량보다 150~200% 증가한 고용량 배터리를 만들어 내는 것이다. 이름은 UHC(Ultra High Capacity) 배터리다. 소재부터 완성품까지, 인동첨단소재→FIC신소재→유로셀로 이어진 3개의 회사가 수직 계열 형태로 구성된 배터리 밸류 체인을 완성했다.”
-앞으로의 계획은 무엇인가.
“배터리는 미래 먹거리다. 배터리를 가진 자가 세상을 지배한다고 해도 과언이 아닐 만큼 배터리의 중요성이 커지고 있다. 음극재 사업을 신성장 동력으로 삼고 3사의 상호 보완적인 기술과 장점을 기반으로 시너지를 강화해 나갈 계획이다. 이미 우리의 분쇄 기술을 활용해 제조한 배터리 성능이 기존 배터리보다 200% 우수하다는 것을 인정받았다. 이제 남은 것은 시제품 생산이다. FIC신소재는 5월 9일 포항에 월 200톤 규모의 실리콘 흑연 복합 음극재 생산 라인 준공을 완료하고 파일럿 라인 가동에 돌입했다. 해외 시장에 진출하기 위한 파트너십도 현재 진행 중이다. 지난 4월엔 영국의 국영 배터리 기관인 영국 배터리산업화센터(UKBIC)의 초청을 받았다. 이 기관은 주로 시제품 단계의 제품들을 대량 양산이 가능하도록 지원하는 사업을 진행하는데, 제조 공정과 시제품 일정에 대한 이야기를 나눴다. 이제 남은 것은 설비를 최대한 늘려 대규모 생산이 가능하도록 하는 것뿐이다.”
☞약력
인동첨단소재 대표이사 회장으로 2차전지 사업의 공격적인 확장을 진두지휘하고 있다. 인동첨단소재·에프아이씨신소재·유로셀의 대표이사를 역임하며 2차전지 소재·음극재·완성품에 이르는 배터리 밸류 체인을 수직 계열화했다.
정채희 기자 poof34@hankyung.com
© 매거진한경, 무단전재 및 재배포 금지