고장력 강판 개발로 연간 294만 톤 CO2 감축, 전사 관리 체제 가동
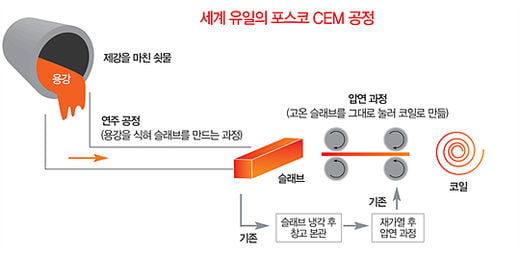
한국을 대표하는 철강 기업인 포스코그룹도 마찬가지다. 포스코는 일찍부터 ‘환경 경영’에 많은 관심을 기울여 왔다. 포스코는 환경 경영의 글로벌 스탠더드를 구현하기 위해 ‘통합 환경 경영 체제’, ‘환경 리스크 관리, ‘열린 커뮤니케이션’의 3대 추진 전략을 세웠다. 이를 기반으로 그룹 차원의 환경 경영 체제 구축, 지속적 환경 개선, 저탄소 녹색 성장 선도, 생태 효율성 향상 등 9대 실천 과제를 추진하고 있다.
이에 따라 포스코는 주요 28개 출자사에 대한 ISO-14001(환경 관리 체제) 인증 획득을 추진하는 동시에 포스코형 환경 경영 인증 제도인 ‘그린-PCP’를 자체 개발해 적용하고 있다. 또 포스코는 철강 산업의 환경 이슈에 대한 국제 협력과 정보 교류를 위해 국제철강협회를 비롯한 국내외 협회, 학회 활동에 참가하고 있으며 글로벌 철강 업체와 기술 교류를 통해 신환경 기술을 공유하고 있다.
첨단 CDQ 설비 도입률 100%
구체적으로 보면 포스코는 발전설비의 고효율화에 가장 큰 노력을 기울이고 있다. 철강 산업이 많은 에너지를 필요로 하는 이유는 철광석을 녹여 쇳물을 만들어야 하기 때문이다. 그래서 포스코를 비롯한 주요 철강사들은 쇳물을 만드는 고로의 온도를 높이기 위해 전기 등의 에너지를 사용한다. 이 때문에 주요 철강사들이 전기를 자체 생산한다. 포스코 역시 발전설비를 가동하고 있다. 즉 포스코는 에너지의 발전 단계부터 효율성을 높이기 위해 발전설비의 고효율화를 꾀하고 있는 것이다.
포스코는 이미 2007년 부생가스를 활용한 ‘고효율 복합발전설비’를 도입했다. 가스터빈의 연소 후 배출되는 고온·고압의 가스를 발전에 재활용하는 것이다. 포스코는 이 설비를 도입해 발전 효율을 37%에서 45%까지 끌어올렸다. 그 결과 146MW의 이 설비는 연간 8만 톤의 이산화탄소(CO₂)를 감축하는 결과를 냈다.
또 작년과 올해에는 배관망을 재구성해 탄소를 대폭 절감하는 효과를 냈다. 기본적으로 공장이 커지면 발생되는 탄소량은 늘어난다. 특히 발전 과정에서는 부생가스가 새나가며 탄소 배출이 증가한다. 포스코는 복합 발전설비를 활용하는 동시에 부생가스가 새나가는 길목을 막는 데 힘을 기울였다. 무려 2.2km에 달하는 배관을 재배치하거나 새로 만들어 새나가는 가스를 막았다. 포스코는 이 같은 과정을 통해 연간 16만 톤의 CO₂를 감축하는 결과를 냈다.
발전 과정뿐만 아니라 생산 과정에서도 적극적으로 CDQ(코크스 건식 소화 설비)를 도입해 에너지를 절감했다. 코크스는 일종의 석탄이다. 철을 만들 때에는 코크스를 섞어 철의 순도를 높인다. CDQ는 코크스를 약 영상 1000도로 녹인 후 다시 영상 200도까지 온도를 낮추는 냉각 설비다. 특히 CDQ는 코크스의 냉각 과정에서 발생하는 폐열을 회수해 전력 및 저압증기를 생산해 낸다. 현재 포스코는 모든 코크스 생산 공정에 CDQ 설비를 도입해 운영 중이다. 글로벌 CDQ의 도입률은 아시아태평양 5개국(캐나다·호주·중국·인도·일본)이 크게는 91%에서 작게는 19%에 불과하다. 하지만 포스코의 CDQ 도입률은 100%다. 포스코 측에 따르면 CDQ 1기당 CO₂의 감축 효과는 연간 14만 톤에 달한다.
포스코는 또 생산 과정에서 적극적으로 CEM(Compact Endless casting and rolling Mill)을 도입해 탄소 배출을 줄이고 있다. CEM은 세계 철강사 중 유일하게 포스코만이 가지고 있는 기술이다. 쇳물로 만든 고온 슬래브(철강 반제품)를 상온으로 식히지 않고 그대로 압연해 바로 코일을 만들어 내는 기술이다.
이 방식을 활용하면 대폭적인 에너지 감축과 투자비를 절감할 수 있다. 압연 과정에서 줄어드는 에너지는 40~50%에 달한다. 그 결과 CO₂의 배출량은 기존 공정에 비해 15%나 줄일 수 있다. 또한 초기 설비투자 비용 역시 15% 줄일 수 있다.
모든 사업 과정에서 CO₂ 관리
포스코는 관리 및 회계 단계에서도 에너지 관리에 많은 노력을 기울인다. 2006년 도입한 ‘전사 온실가스 관리 시스템’이 대표적 사례다. 이 시스템은 국제 온실가스 배출량 산정 기준에 따라 구축됐는데 쉽게 생각해 모든 사업과정에서 CO₂를 관리하는 것이다. 포스코는 ‘전사·사업장·단위공장’별로 CO₂ 배출 책임을 구분한다. 또 발전 단계나 부생가스 발생 단계에도 각각 CO₂ 배출 책임량을 부여한다. 부여된 책임량은 본사 및 각 사업장의 실무자가 1일 단위로 관리하게 된다. 특히 최근 들어서는 관리 시스템에 정보통신기술(ICT)을 접목해 더욱 효율적이고 치밀한 관리를 추진하고 있다.
또 철광석이나 석탄의 가격 변동처럼 ‘온실가스 초과 배출 및 감축’을 비용과 수익으로 환산해 조업 원가에 반영 중이다. 또한 2014년부터 배출권 거래제 시행에 따라 회계 장부에 ‘배출 부채’를 산입해 회계 처리를 하고 있다.
마지막으로 포스코는 제품 자체에 ‘친환경 기술’을 녹여 내기 위해 많은 노력을 하고 있다. 대표적인 제품이 고장력 자동차 강판이다. 고장력 자동차 강판은 일반 강판 대비 얇은 두께에도 고강도를 얻을 수 있는 제품이다. 포스코의 분석에 따르면 고장력 강판 1톤당 줄어드는 온실가스는 연간 0.8톤에 달한다. 이유는 일반 강에 비해 20%나 가벼워 이 강판을 적용한 자동차는 무게가 5% 정도 줄어들기 때문이다. 자동차의 무게는 연비와 직결된다. 최근 자동차의 연비를 감안하면 1대당 연간 185kg의 CO₂ 감축 효과가 있다. 그 결과 포스코는 고장력 강판의 개발 및 판매 확대로 2014년 기준 연간 294만 톤의 온실가스 감축에 기여한 것으로 분석된다. 또 ‘포스멘트’를 통한 그린 빌딩으로 CO₂ 감축에 기여한다. 포스멘트는 철강 생산 과정에서 나오는 시멘트다. 기존의 시멘트에 비해 압축 강도가 세고 염분이나 불에 훨씬 강하다. 이 때문에 균열이 발생하기 쉬운 발전소 등의 대형 구조물이나 해안 구조물에 쓰인다. 포스멘트를 건설 현장에 적용하면 일반 슬래그 시멘트보다 약 60%의 탄소를 절감할 수 있다. 포스코는 포스멘트의 판매량을 2012년 7000톤에서 2015년 98만 톤까지 대폭 늘렸다.
박헌 포스코 환경사회공헌실장은 “결국 온실가스 절감의 핵심은 기술 개발”이라면서 “정부의 규제 정책은 상용화가 완료된 기술 도입을 유도하는 데 한정하는 한편 신기술 개발이나 시험 설비투자를 위한 지원 정책을 확대하면 기업이 더 효율적으로 온실가스를 절감할 수 있을 것”이라고 강조했다.
이홍표 기자 hawlling@hankyung.com
‘재활용으로 만든 신연료’ 개발 중
포스코는 새로운 연료로 주목받게 될 ‘쓰레기로 만든 메탄가스’를 연구하는 데 집중하고 있다. 메탄가스는 이산화탄소(CO₂)보다 약 25배 더 강력한 온실효과를 내는 물질이다. 하지만 포스코에너지는 메탄가스가 연로로 쓰이는 액화천연가스(LNG)와 압축천연가스(CNG)의 주성분이라는 데 초점을 맞췄다. 쓰레기를 발효해 얻어 낸 합성가스에서 메탄가스를 추출해 에너지로 사용하자는 것이다. 포스코에너지는 현재 네덜란드 ECN에서 개발한 폐자원 가스화 기술이 한국에 적용 가능한지 실험을 통해 검증하는 중이다. 이 실증 단계는 2017년까지 완료될 예정이다.
본격적으로 사업이 시작되면 폐자원 가스화를 통해 얻은 메탄가스는 다양한 용도로 쓰일 수 있다. 기본적으로 LNG 발전소나 CNG 차량 연료로 대체할 수 있다. 또 가스화 과정에서 나온 수소는 연료전지 발전에, 일산화탄소는 섬유나 플라스틱 등의 화학 공정에 쓸 수 있다.
폐자원 가스화 기술은 쓰레기 발생량이 하루 160톤 이상이면 적용할 수 있다. 포스코에너지는 “(폐자원 가스화 기술은) 우수한 발전 효율로 폐기량 발생량이 하루 160톤 이상을 유지하는 국내 36개 지자체를 대상으로 사업을 할 수 있을 것”이라고 밝혔다.
© 매거진한경, 무단전재 및 재배포 금지