돼지털·가발 수출하던 한국
50년 만에 세계 조선시장 제패
혁신 기술로 패러다임 전환 이끌어
추격자에서 선도자로 우뚝
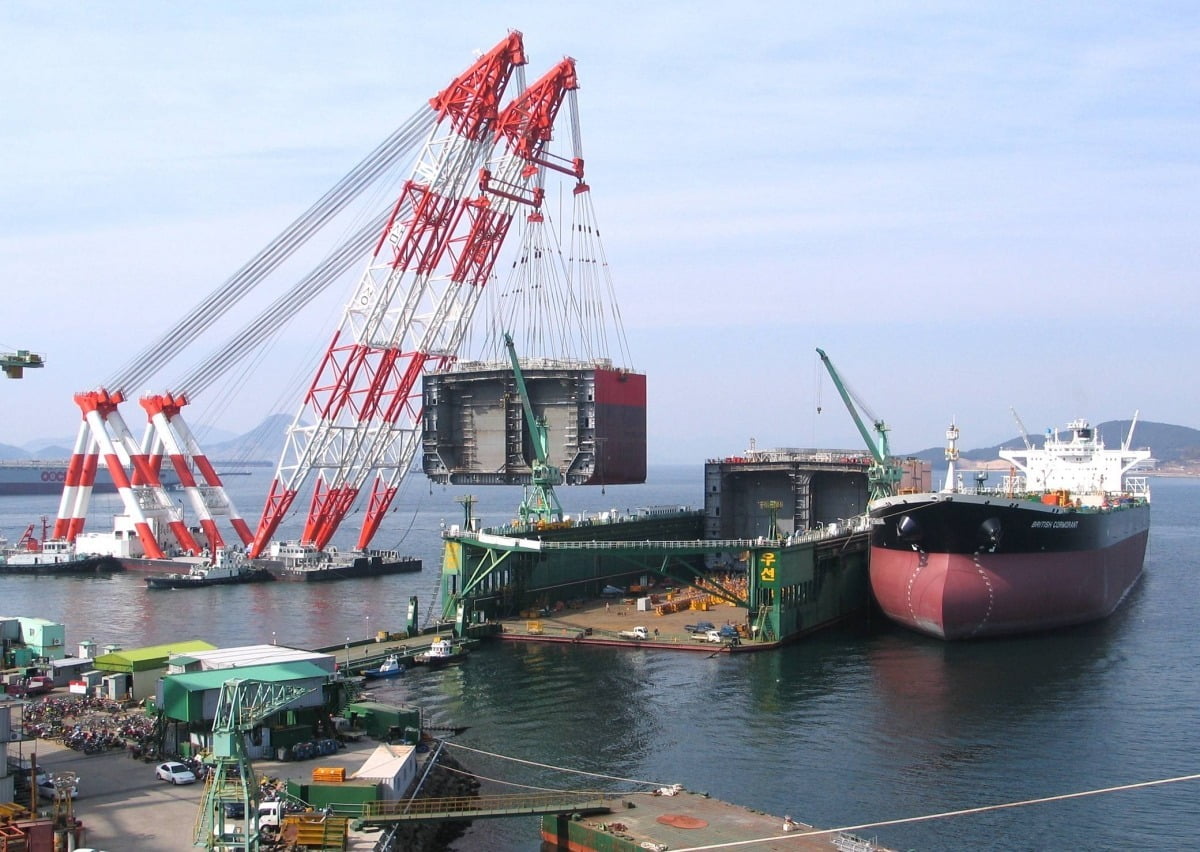
수출의 버팀목 역할을 해왔던 반도체의 부진 속에서 조선업이 새로운 수출 효자로 떠오르고 있다. 새로 건조된 선박의 가격도 15년 만에 최고치다. 영국의 조선·해운 시황 분석 기관 클락슨리서치에 따르면 6월 신조선가지수는 170.76을 기록해 2020년 말(125.50) 대비 36% 상승했다. 신조선가지수가 170을 웃돈 기간은 조선업 슈퍼사이클 시기였던 2007년 4월부터 2008년 12월(177.97)뿐이었다.
국제해사기구(IMO)의 환경 규제 강화로 한국이 세계 1위 점유율을 유지하고 있는 고부가·친환경 선박의 발주량도 급증하고 있다. 한국은 고부가·친환경 선박 시장에서도 1분기 70% 이상 점유율을 차지하며 세계 1위 위상을 이어 가고 있다. 저가 수주 지양, 선가 상승, IMO 환경 규제 강화 등이 맞물리면서 한국 조선업계는 역대급 수주 호황을 누리고 있다.
HD한국조선해양·삼성중공업·한화오션(구 대우조선해양) 등 조선 빅3의 2분기 실적 기대감도 커지고 있다. 업계에선 3차 슈퍼사이클 초입에 진입했다는 분석이 나오고 있다. 1970년대부터 50여 년간 위기를 기회로 바꾸며 쉼 없이 달려온 한국 조선업 역사를 살펴봤다.
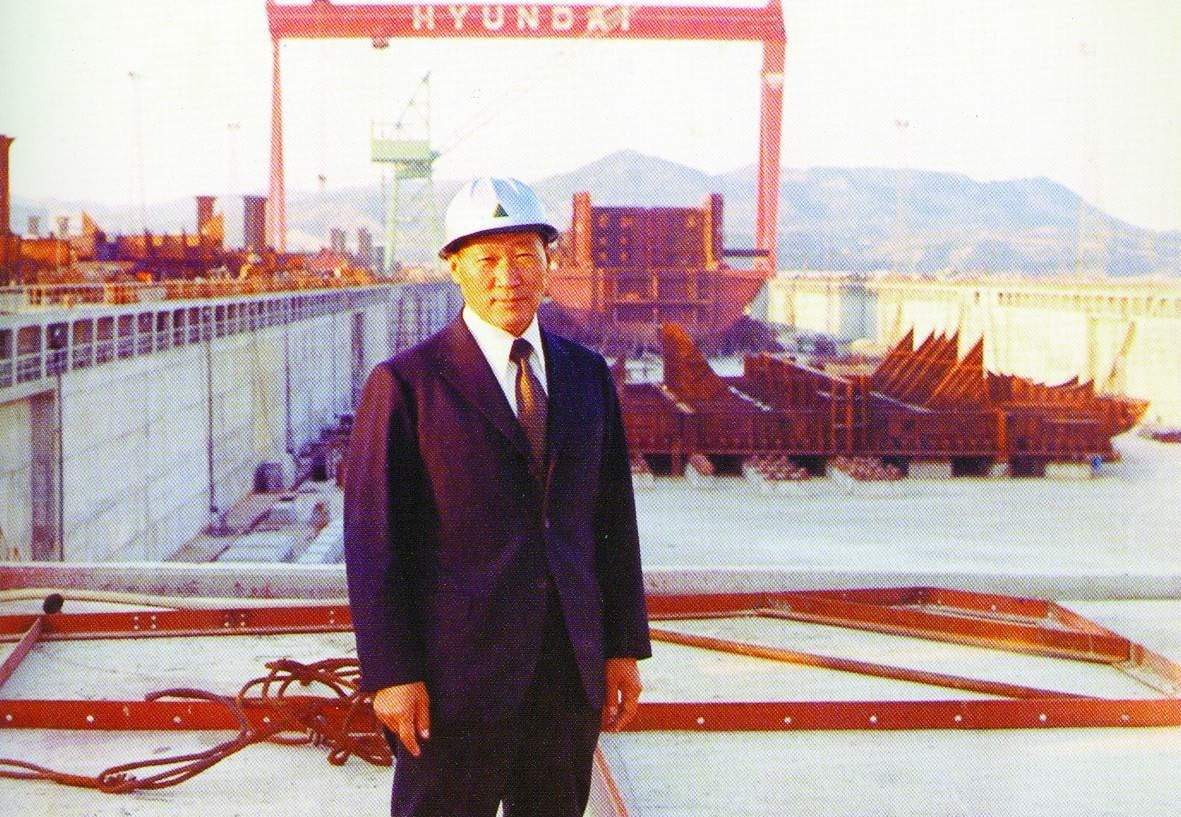
조선업은 호황과 불황이 주기적으로 반복되는 사이클 산업이다. 조선업은 30년 주기로 슈퍼사이클을 맞았다. 1·2차 슈퍼사이클은 1973년과 2003년이었다. 사이클이 반복될 때마다 조선업의 패권국이 바뀌어 왔다.
세계 조선산업의 중심은 한국과 중국, 일본을 중심으로 한 동아시아 지역이다. 조선업 세계 1위 자리는 1940년대 영국, 1950년대 서유럽, 1960~1980년대 일본, 1990년부터 한국으로 변했다. 현재 중국의 추격이 계속되며 한국 조선소들과 중국 조선소들 간의 패권 다툼이 치열해지고 있다.
지금은 세계 조선 시장을 호령하고 있지만 50여 년 전인 1960년대만 해도 한국은 기술도, 자원도, 자본도 없었다. 외화 벌이를 위해 돼지털·마른오징어·자작나무 등 팔 수 있는 것은 모두 내다 팔아야 했다. 여성들은 머리카락을 잘라 가발을 만들어 수출에 힘을 보탰다.
1970년대 박정희 대통령은 수출 100억 달러, 1인당 국민소득 1000달러 달성이라는 목표를 세웠는데 기존의 경공업 중심 산업과 수출 구조로는 불가능했다. 산업 체질을 바꾸기 위해 정부 주도로 1973년 중화학 공업화 정책을 추진하면서 조선업 육성을 본격화했다.
박정희 대통령은 한국 조선업을 개척할 인물로 현대그룹 창업자인 정주영 회장을 점찍었다. 당시 한국 조선업계의 세계 시장점유율은 1%에도 못 미쳤다. 정주영 회장은 조선소도, 기술도, 자본도 없는 상태에서 500원짜리 지폐 속 거북선과 울산 미포만 백사장 사진을 내보이는 기지를 발휘해 외국 투자 자금을 유치하며 조선업 성공 신화를 썼다.
‘리벳’ 영국→‘용접’ 일본→‘독’ 한국
조선업 패권 이동
20세기 들어 조선업 패권이 이동할 때마다 혁신 기술이 등장했다. 제2차 세계대전 이전까지만 해도 영국은 세계 조선업의 절대 강자였다. 산업혁명과 증기선의 발명 이후 근대 조선 산업의 기틀을 만든 영국은 ‘리벳 공법’을 앞세워 19~20세기 전 세계 해상 패권을 장악했다.
지금은 글로벌 선박 시장 경쟁에서 뒤처져 있지만 20세기 초반까지만 하더라도 글로벌 선박 건조의 약 60%를 차지하기도 했다. 목선에서 철선으로 넘어가는 시기에 등장한 리벳 공법은 철판 2장을 겹쳐 구멍을 뚫은 뒤 굵은 못인 리벳(rivet)을 꽂아 접합하는 건조 기술이다.
이 기술로 제1차 세계대전의 전함 수요를 선점한 영국은 20세기 중반까지 100년 이상 조선업 최강자 자리를 지켰다. 1970년 보험업자들이 만든 영국 로이드선급(RL)의 조선 규칙이 현재까지도 전 세계적인 국제 기준으로 통용되는 이유다.
영국의 리벳 공법을 밀어낸 것은 일본의 ‘용접 공법’이었다. 일본은 1953년 미국에서 군수용으로 사용되던 용접·블록 기술을 전수 받아 도약의 발판을 마련했다. 선체를 여러 블록으로 나눠 각각 만든 뒤 이를 용접하는 방식으로 생산성을 3배 이상 끌어올린 일본은 원가 우위를 앞세워 1970년대 초 1차 오일쇼크로 폭증한 유조선 수요를 싹쓸이하면서 세계 조선 산업의 주도권을 가져왔다.
하지만 일본의 패권은 오래가지 않았다. 1972년 2차 오일쇼크로 조선업이 장기 침체에 빠지자 독(dock)의 절반을 닫고 인력 감축을 단행했다. 축소 사이클 국면에서 일본 정부는 노동 집약적인 조선업을 사양 산업으로 판단했다. 1978~1980년, 1987~1988년 두 차례에 걸쳐 구조 조정(조선 합리화 정책)을 하는 과정에서 핵심 설계 인력이 대거 유출됐다.
비용 절감에 급급해 표준화된 선박 제조에 매달렸다. 하지만 이는 선주의 다양한 요구 사항을 신속하게 설계에 반영해 한 척씩 주문 제작하는 조선업의 특성을 간과한 오판이었다. 일본은 결국 과도한 인력 구조 조정과 선주들의 요구에 부응하는 다양한 선박 제조 역량을 확보하지 못해 경쟁력을 상실하게 된다.
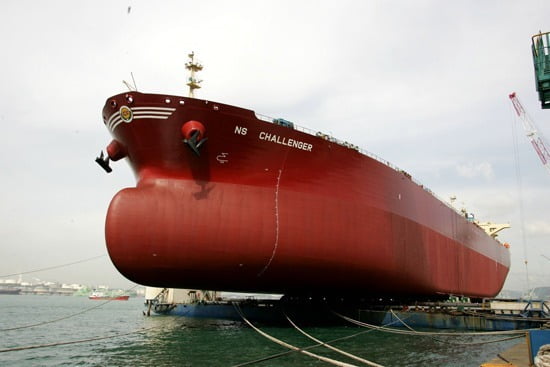
조선업 후발 주자였던 한국은 투자를 축소하던 일본과 반대로 1990년대 초부터 과감한 설비 투자에 집중해 세계 1위로 도약한다. 다시 찾아온 호황 사이클에서 전 세계에서 밀려드는 수주 물량에 대응하기 위해 한국이 꺼내든 무기는 ‘독의 혁신’이었다.
1994년 삼성중공업은 3000억원을 들여 경남 거제에 셋째 독을 완공했고 HD현대중공업은 당시 울산에 여덟째 독과 아홉째 독을 만들며 생산 능력을 확대했다. 연구·개발(R&D)에 대한 투자가 늘면서 기술 경쟁력을 한 차원 끌어올린 신공법들도 대거 선보였다.
삼성중공업은 2001년 세계 최초로 육지에서 만든 대형 선박 블록을 바다 위에 떠 있는 작업대로 옮겨 건조한 뒤 작업대를 가라앉혀 진수하는 ‘플로팅 독’ 방식을 개발했다. ‘배는 독에서 만들어야 한다’는 조선업계의 기본 상식을 깬 것이다.
8층 건물 크기의 대형 철구조물이 벽돌을 끼워 맞추듯 조립되는 기술인 ‘메가블록 공법’도 개발했다. 400∼500톤인 기존 소형 블록을 무게 3000톤짜리 8층 건물 크기로 대형화해 건조 기간을 줄이는 공법이다.
HD현대중공업은 2001년 세계 최초의 무(無) 독 건조 방식인 ‘육상 건조 기법’을 도입했다. 육상에서 배를 건조한 다음 해상 플로팅 독으로 이동시킨 후 진수해 선박을 건조하는 방식이다.
2008년엔 ‘독 하나에 배 한 척’이란 고정관념을 깬 ‘탠덤 침수 공법’을 개발했다. 한 독 안에 2척 이상의 선박을 동시에 건조하는 공법으로 공간의 한계를 극복한 것이다. 수백억원이 드는독크의 확장 없이도 공기를 단축할 수 있어 생산성을 높일 수 있었다.
대우조선해양(한화오션)은 2대의 해상 크레인을 연결해 6000톤급 대형 블록을 한 번에 들어 올리는 신공법을 개발했다. 설비 한계를 극복해 3주 정도 독의 공기를 단축할 수 있었고 경비 절감 효과도 거뒀다. 작업 기간 단축으로 독 회전율이 높아져 매출 극대화는 물론 건조 기간도 앞당길 수 있었다.
한국은 초대형 독과 우수한 건조 기술력을 바탕으로 1990년대 중반 이후 찾아온 조선업 활황기의 수주 증가에 적극 대응하며 세계 시장을 휩쓸기 시작했다. 다양한 신공법과 신기술로 조선 분야의 수주 경쟁력을 강화한 한국 조선업은 신규 수주, 건조량, 수주 잔량 등 실적 면에서도 경쟁국들을 압도하게 됐고 1999년 수주량 기준으로 일본을 제치고 조선 세계 1위에 올라선 뒤로 현재까지 선두를 이어 가고 있다.
안옥희 기자 ahnoh05@hankyung.com
© 매거진한경, 무단전재 및 재배포 금지